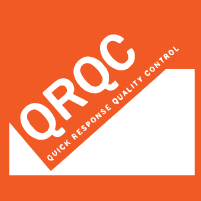
Le QRQC - Quick Response Quality Control
Qu'est-ce que le QRQC ?
Quelle est l'origine du QRQC ?
Le QRQC a été inspiré par le Lean Management et est issu du Toyota Production System formalisé par Ohno Taiichi en 1978.
Qu'est-ce que le QRQC ?
C'est un mélange d'attitudes et de management qui s'appuie sur des outils qualités.
L'abréviation QRQC signifie "Quick Response Quality Control". La traduction française serait : "Contrôle Qualité avec Réponse Rapide".
A quoi sert le QRQC ?
Le QRQC répond au besoin d'amélioration permanente. Cette démarche est fondée sur deux orientations : la vitesse et la maîtrise. En effet, le QRQC permet de réconcilier la vitesse d'exécution à court terme de la résolution de problème et la maîtrise complète des processus de production.
Les fondements du QRQC
Le quality response : la vitesse
La vitesse est un élément important de la démarche de résolution de problème. En effet, pendant toute la durée du problème, il y a des coûts de non-qualité qui se cumulent. Ainsi chaque heure de perdues dans la résolution de problème coûte cher à l'entreprise.
Un autre enjeu est de résoudre les problèmes dans un délais court pour que des résultats positifs soient rapidement visible. Cela permet de motiver davantage les acteurs de la résolution de problème puisque ceux-ci peuvent voir des résultats concrets sans attendre.
Il ne faut toutefois pas confondre vitesse et précipitation. Il ne faut pas que l'exigence de vitesse se fasse au détriment de la qualité des résultats de résolution de problème.
Dans la démarche, il y a six notions de temporalité différentes :
- 4 à 6 heures, qui constituent les actions immédiates d'identification et de sécurisation
- 24 heures, pour les actions de confinement et action curatives
- 5 à 7 jours, pour l'analyse et les actions correctives
- 10 jours, pour la généralisation des actions correctives par de la transversalité et la mise en œuvre d'actions préventives
- 30 jours, pour la boucle d'apprentissage et la mise en œuvre des audits de verrouillage des actions entreprises.
Les durées doivent apparaître comme des point de référence et des cibles à viser. Il faut être conscient que certaines actions nécessitent un délai plus long, en particulier celles qui demandent un investissement financier important ou impliquent des modifications plus longues. Cela peut être par exemple de nouvelles études de construction dans un nouveau matériau par exemple. Dans ces cas-là, il ne faut, en effet, pas considérer comme des échecs des temps de réalisation plus longs que les 5 à 7 jours d'analyse.
Dans ce cas de figure, il faut mettre l'accent sur l'obligation de moyens et s'assurer que l'énergie dans le traitement est allouée à la juste proportion de l'importance du problème.
Les actions sous 4h à 6h
Dans cette temporalité, le principe de l'arrêt au premier défaut doit être mis en application. Pour cela, on peut appliquer les principes de l'Andon et du Jidoka. En effet, une réaction rapide permet de se rendre immédiatement sur le terrain et de faire des constats en temps réel.
Le management doit avoir responsabilisé les opérateurs dans la prise de décision de l'arrêt de la production. Il doit également les soutenir dans cette pratique qui consiste à rendre visible le problème et à le partager immédiatement.
Cela est contre-intuitif pour le management à première vue puisque les outils de productions doivent être arrêtés et que cet arrêt impact dirctement les indicateurs de productivité. Le management doit donc, même si cela va à l'encontre de la productivité à court terme, encourager les arrêts de ligne si nécessaire car cela est bénéfique sur le long terme.
Il s'agit ici de mener des actions de sécurisation permettant d'empêcher la propagation du pblème en bloquant les flux logistiques concernés et en isolant les produits "contaminés"
L'étendue de cette action de confinement ne doit pas s'arrêter à la simple ligne de production, mais doit aller en aval et en amont de l'opération qui est concernée. Cela veut dire du fournisseur initial jusqu'au produit fini déjà livré au client.
Il s'agit ici d'actions de confinement des produits à risque.
Les actions sous 24 heures
Dans cette temporalité, il convient de mettre en œuvre les actions de sécurisation des clients qu'elles soient internes ou externes. Cela passera par des opérations d'identification précise du problème, des opérations de remise en état si cela est possible et pertinent ou encore d'opérations de tri.
Les actions sous 5 à 7 jours
Il s'agit de réaliser l'analyse de cause et de mettre en œuvre les actions correctives qui permettront de corriger durablement le problème.
Les actions sous 10 jours
Il s'agit là de généraliser les actions correctives. C'est grâce à ses actions de généralisation que l'on éradique le problème sur le long terme. Il s'agit d'opérer dans la transversalité en recherchant les situations similaires dans l'entreprise. Par exemple, sur une autre famille de produit ou sur un autre process similaire.
Pour cette étape, il est important de réaliser une analyse produit et process.
Les actions sous 30 jours
Il s'agit là de s'assurer de l'efficacité sur le moyen terme des actions correctives et d'ancrer les pratiques.
La généralisation doit se terminer par un apprentissage à partir des erreurs passées. Cet apprentissage peut amener à établir de nouveaux standards. En effet, les standards sont la cale anti-retour de l'amélioration. Par la formalisation des nouvelles pratiques, il devient possible de réaliser des audits et de formuler de nouvelles hypothèses d'amélioration.
Le quality control: la maîtrise
Le contrôle qualité ou plus précisément la maîtrise qualité.
La rigueur
Il s'agit là de l'exigence de discipline et du respect des règles établies.
La mise en œuvre du QRQC se fait selon un cadre extrêmement précis qui doit être respecté au quotidien. La ponctualité, le respect et la méthode doivent impérativement être dans les fondements de mise en place de la démarche.
Vérifications
Il s'agit là de vérifier les engagements pris. La vérification des engagements est un gage de fiabilité et de pérennité des actions mises en œuvre.
Le processus QRQC
ETAPE 1 : la détection du problème
L'arrêt au premier défaut
La détection de problème est une première étape déterminante dans le succès de la résolution de problème. Il est, en effet, indispensable d'avoir la connaissance des problèmes de façon à pouvoir les sélectionner et les traiter.
L'arrêt au premier défaut ou jidoka est un élément déterminant de la résolution de problème. En effet, dès que l'on détecte un défaut et que l'on s'arrête, on est capable d'identifier directement l'effet du problème. L'analyse est directe et instantanée. Cela permet de gagner un temps considérable dans les phases d'identification du problème, de recherche de la cause et de recherche de solutions.
Dispositifs d’identification
Il est important de conserver les non-conformités détectées. Le plus souvent des boîtes rouges seront utilisées pour isoler la pièce. Afin de s'assurer d'avoir à disposition le genbutsu (la pièce réelle), il est important que le système d'identification soit parfait.
Le fait que tout le monde voit les mêmes choses au même moment permet également d'obtenir un consensus sur l'effet local du problème. Cela permet également de conserver les preuves du problème et les éléments relatifs aux conditions d'apparition du problème.
L'enregistrement sur tableau QRQC
Le tableau QRQC contient les informations qui permettent de caractériser le problème et d'en faciliter la résolution. Les informations seront :
- Description du problème
- Date et heure d'apparition du problème
- Opérateur qui a détecté le problème
- Cause première identifiée
- Actions immédiates de sécurisation et confinement
- Responsable de l'action
- Délai de mise en œuvre
De manière globale, on trouvera toutes les informations que l'on jugera nécessaires à la résolution du problème. On peut même encourager la présence de croquis dessinés à la main si cela est pertinent.
Nous retrouvons dans cette étape les éléments du QQOQCP .
ETAPE 2 : La communication du problème
La résolution de problème est un enchaînement de tâches qui nécessite une communication et une synchronisation. Pour mener la résolution de problème, il est nécessaire de nommer un chef d'orchestre. Il faut donc assigner le problème à un
pilote.
L'assignation du problème est un acte formel et un engagement du pilote à mener à bien le traitement du problème. L'ensemble de ce processus d'assignation devrait être formalisé et diffusé de façon à ce que les responsabilités soient connues de tous. Le pilote n'est pas le seul à travailler sur le sujet : il va solliciter d'autres personnes ayant les compétences requises à la résolution de problème.
Les réunions QRQC
La réunion QRQC est dirigé par un manager. La durée est fixe. Vous pouvez choisir une 30 minutes qui en général est bien adapté à la plupart des contextes.
L'objectif de ces réunions est de :
- S'assurer que les problèmes sont bien identifiés et remontés au managment
- S'assurer qu'un pilote a bien été désigné pour le traitement de chaque problème
- S'assurer que chaque problème fait bien l'objet d'une analyse et d'actions correctives
- S'assurer qu'un pilote est affecté à chaque action
ETAPE 3 : L'analyse du problème
Pour cette phase, le réflexe est d'adopter une attitude San gen Shugi . Le contact avec le réel est déterminant pour agir efficacement dans l'analyse du problème.
La communication avec l'ensemble des personnes ayant vécu le problème apportera bon nombre d'éléments d'analyse.
Le FTA - Factor Tree Analysis
L'arbre des facteurs a vocation à lister tous les facteurs influants dans la génération du problème et potentiellement dans sa non-détection. L'utilisation des 5M sera utile pour cette analyse.
Étape 4 vérification
Cette étape de vérification consiste non seulement à vérifier que les actions ont réellement été mises en œuvre, mais également que ces actions ont résolues durablement le problème.
Cette étape de vérification va également consister à verrouiller l'ensemble des dispositions prises par de nouveaux standards et l'organisation d'audits.
Perfect QRQC - vol 1 - Les fondations: Quick Response Quality Control
La management qualité basé sur l'attitude San Gen Shugi
Quintin Testa, Hakim Aoudia
Maxima,
10 janv. 2012
196 pages
ISBN 2818806801, 9782818806807
Découvrez nos micro-formations et conseils en:
- Utilisation des outils qualité
- Le contrôle qualité
- Techniques de résolution de problèmes
- Le tableaux de bord qualité
- ... et bien plus encore!
Formations sur mesure adaptées à VOS besoins, disponibles rapidement.
📩Écrivez-nous à: commentprogresser@gmail.com
Nicolas DEROBERT
